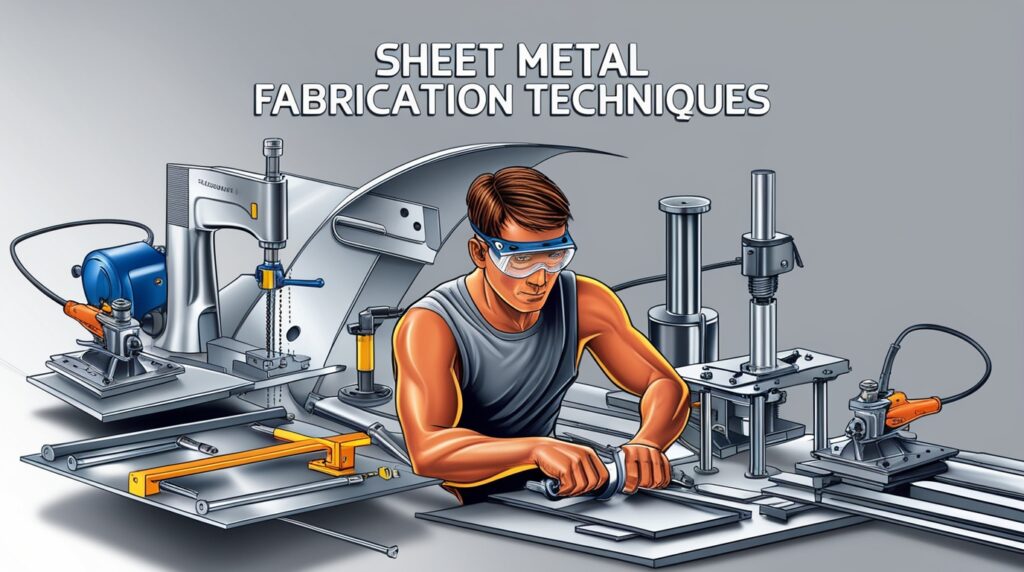
Introduction
Sheet Metal Fabrication Techniques refer to the various processes used to transform flat sheets of metal into intricate components and structures, essential across numerous industries, including automotive, aerospace, electronics, and construction. These techniques, which encompass cutting, forming, and joining methods, play a crucial role in manufacturing, allowing for the creation of both simple and complex designs. The ability to produce customized and high-precision parts efficiently makes sheet metal fabrication a cornerstone of modern production methods and a significant contributor to economic growth in various sectors. Among the prominent techniques employed in sheet metal fabrication are laser cutting, waterjet cutting, and plasma cutting, each offering distinct advantages in terms of precision, material handling, and efficiency.
Forming methods, such as stamping and bending, further enhance the versatility of fabricated products, enabling the creation of specialized shapes and structures. Joining techniques, including welding and mechanical fastening, are equally critical, ensuring the structural integrity of the final assemblies. However, the industry faces challenges such as high initial costs for advanced machinery, design limitations for complex shapes, and the complexities associated with automation.
The selection of materials in sheet metal fabrication is also noteworthy, with aluminum, stainless steel, and copper being among the most commonly used. Each material offers unique properties that cater to specific applications, ranging from lightweight components in the automotive industry to durable structures in construction.
Furthermore, advancements in technology, particularly the integration of Industry 4.0 practices, are transforming the landscape of sheet metal fabrication, enhancing efficiency, customization, and sustainability in manufacturing processes.
In conclusion, while sheet metal fabrication techniques are indispensable for producing a wide array of products, the industry must navigate various challenges and embrace technological advancements to maintain its relevance and efficiency. The ongoing evolution of fabrication practices underscores the importance of innovation and adaptability in meeting the growing demands of diverse markets.
Types of Sheet Metal Fabrication Techniques
Sheet metal fabrication encompasses a variety of processes used to transform flat metal sheets into complex shapes and structures. The primary techniques employed in this field include cutting, forming, and joining methods, each with specific applications and advantages.
Cutting Techniques
Laser Cutting
Laser cutting has revolutionized sheet metal manufacturing by offering unparalleled precision and efficiency. This technique employs a high-powered laser beam, directed through optics, to concentrate energy onto a small area of the metal sheet. The process begins with a CAD file that guides the laser’s path, creating clean, sharp edges by melting or vaporizing the metal as a coaxial gas jet blows away the molten material.
Waterjet Cutting
Waterjet cutting uses a high-pressure pump to force water through a tiny orifice, creating a jet that travels at speeds up to 900 m/s. This technique can cut various materials, including metals and composites, and is capable of handling significant thicknesses, such as aluminum up to 200 mm thick.
Plasma Cutting
Plasma cutting relies on the creation of an electrical arc that ionizes gas, forming plasma capable of melting metal with remarkable speed. While efficient for conductive materials, plasma cutting is less precise for very thin metals and creates a wider heat-affected zone compared to laser cutting.
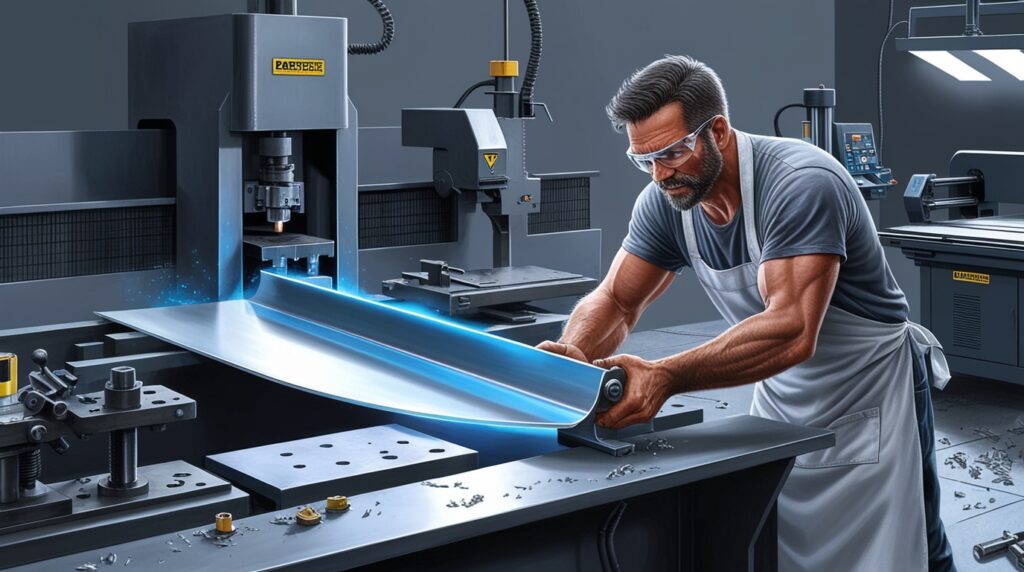
Forming Techniques
Stamping
Stamping involves shaping sheet metal using various processes.
- Progressive Stamping: Utilizes a series of stations in a die set for high-volume production.
- Deep Draw Stamping: Forms deep, cup-shaped parts suitable for items like beverage cans.
- Fine Blanking: Produces parts with clean-cut edges, eliminating the need for secondary operations.
Joining Techniques
Welding
Several welding methods are commonly used in sheet metal fabrication, including:
- Tungsten Inert Gas (TIG) Welding: Ideal for thin sheet metal and non-ferrous materials, offering high-quality welds.
- Resistance Spot Welding: Creates localized fusion between overlapping sheets, widely used in automotive manufacturing.
- Seam Welding: Produces continuous welds for leak-tight joints in tanks and containers.
Adhesive Bonding
Adhesive bonding combines mechanical fastening with adhesive techniques. It leverages properties such as surface wetting and curing to create strong and durable connections. Advanced adhesive technologies, including structural adhesives and hybrid joining methods, are increasingly utilized to enhance joint performance and assembly efficiency.
Mechanical Fastening
Mechanical fastening techniques include self-piercing rivets (SPR), clinching, flow drill screwing, and adhesive-bonded fasteners. These methods are particularly useful for joining dissimilar materials while minimizing material distortion. These various techniques enable manufacturers to create everything from simple components to intricate assemblies, catering to diverse industrial and commercial applications. Understanding these methods is essential for optimizing the fabrication process and achieving desired product specifications.
Materials Used in Sheet Metal Fabrication
Aluminum is favored for its lightweight properties and excellent strength-to-weight ratio, making it ideal for various sheet metal applications. The most notable aluminum alloys for fabrication include aluminum 5052 and aluminum 6061, which are well-suited for tasks requiring machinability and corrosion resistance. Applications range from automotive and aircraft parts to food packaging, electronic products, kitchenware, and medical equipment. Additionally, aluminum’s conductivity of heat and electricity makes it a prime choice in the electronics sector.
Steel
Steel is another crucial material in sheet metal fabrication, particularly known for its strength and durability. It is often classified into two types: hot rolled and cold rolled. Cold rolled steel is about 20% stronger than hot rolled steel and is preferred for applications where finish quality is essential, such as automotive parts and home appliances. Conversely, hot rolled steel, processed at high temperatures, is cost-effective and easy to fabricate, typically used in applications where surface finish is not a priority.
Stainless Steel
Stainless steel is renowned for its corrosion resistance, making it an ideal material for kitchen utensils, medical equipment, and other products that require hygiene and durability.
Copper and Brass
Copper and brass are also integral to sheet metal fabrication. Copper is widely used in electrical engineering and cookware due to its excellent conductivity. Brass, an alloy of copper and zinc, is valued for its workability and aesthetic appeal, commonly found in decorative applications and plumbing.
Pre-Plated Steel
Pre-plated steel, which is galvanized sheet metal coated with zinc, offers enhanced corrosion resistance. This type of steel ensures greater formability and weldability, making it suitable for the production of equipment bodies.
Material Selection Considerations
When selecting materials for sheet metal fabrication, various properties are essential, including strength, conductivity, hardness, flexibility, and resistance to corrosion. These properties are crucial for ensuring the longevity and performance of the fabricated components. As such, the choice of material greatly influences the efficiency and effectiveness of the overall fabrication process, allowing manufacturers to produce a diverse range of products from light-duty applications to heavy-duty structural components.
Tools and Equipment
To carry out sheet metal fabrication, a variety of tools and equipment are essential for achieving precision and efficiency in the manufacturing process. These tools range from cutting machines to welding equipment, each serving a specific function in the fabrication workflow.
Cutting Tools
Precision cutting is fundamental in sheet metal fabrication. Advanced tools such as laser cutters, waterjets, and plasma cutters are utilized for their ability to deliver clean cuts while minimizing material waste. These technologies enable manufacturers to execute intricate designs and shapes with high accuracy. For simpler cutting tasks, shears and punch presses are commonly employed to streamline the process
Bending and Forming Equipment
Press brakes are pivotal machines used for bending metal sheets into specified angles, curves, and shapes, adhering closely to design specifications. Roll forming equipment is also crucial, particularly for shaping long strips of metal into cylindrical forms, such as pipes and tubes. CNC bending machines further enhance this process by automating the bending, ensuring precise control over dimensions and angles
Joining and Welding Tools
Welding and joining tools, including TIG, MIG, and spot welding equipment, are essential for assembling metal pieces, ensuring structural integrity and durability in the final product. These methods are critical for creating robust connections between fabricated components.
Finishing Tools
Finishing tools such as grinders, sanders, and polishers are employed to give the fabricated metal its final surface finish. These tools enhance the aesthetics of the product while removing any imperfections that may have occurred during the fabrication process. Additionally, tools like stamps and matting tools provide texture and design features to the metal surfaces, allowing for creative expression in the final product
Automation and Robotics
The incorporation of automation and robotics in sheet metal fabrication has revolutionized the industry, enabling manufacturers to scale production quickly and efficiently without increasing labor costs. Automatic loaders and unloaders, alongside collaborative robots (cobots), facilitate tasks such as press tending and assembly, enhancing speed and productivity. In-house technical expertise remains crucial for developing these robotic operations, ensuring effective implementation and ongoing support
Applications of Sheet Metal Fabrication
Sheet metal fabrication serves a wide range of industries due to its versatility and efficiency in producing high-quality metal components. This section outlines the primary applications across various sectors.
Electronics
The electronics industry utilizes sheet metal fabrication for the rapid prototyping and production of components found in devices like computers, smartphones, and telecommunications equipment. Techniques such as laser and waterjet cutting are favored for their ability to produce intricate parts quickly and cost-effectively. This efficiency facilitates faster examination of prototypes, enabling manufacturers to bring products to market more swiftly.
Healthcare
In the healthcare sector, sheet metal fabrication is crucial for manufacturing precise and high-quality medical tools. The materials commonly used, such as aluminum and stainless steel, are ideal for applications like MRI machines as they do not interfere with magnetic fields. Moreover, surgical instruments, including scalpels and specialized tools, benefit from the accuracy provided by sheet metal fabrication processes, which can identify design flaws and facilitate necessary adjustments.
Appliances
The appliance industry heavily relies on sheet metal fabrication, with nearly every appliance incorporating some form of metal. The fabrication processes ensure that components like blender housings, capillary tubes, and other kitchen appliances meet strict specifications and tolerances. The advanced techniques available allow for the design and production of durable yet lightweight enclosures and inner parts, contributing to the overall quality of consumer products.
Automotive
Automotive manufacturing significantly benefits from sheet metal fabrication, which enables the creation of essential vehicle components such as fenders, hoods, roofs, and side panels. These parts are typically produced through processes like laser cutting and stamping, contributing to the overall structural integrity of vehicles while maintaining a lightweight profile. The ability to form strong frames from thin sheets of metal has revolutionized automotive design.
Structural Engineering
Structural sheet metal fabrication plays a vital role in construction, producing metal components used in building frameworks, siding, roofing, and load-bearing structures. The processes involved are designed to ensure high strength and durability, making them indispensable in large-scale construction projects.
Custom Manufacturing
With the rise of consumer demand for personalized products, sheet metal fabrication has adapted through the integration of advanced digital tools for customization. Technologies like computer-aided design (CAD) and computer-aided manufacturing (CAM) are increasingly utilized to streamline production processes, allowing for on-demand manufacturing that meets specific customer needs.
Advantages and Disadvantages
Sheet metal fabrication encompasses a diverse range of processes and techniques, each presenting its unique set of advantages and disadvantages. Understanding these factors is crucial for manufacturers to determine the most suitable applications for their projects.
Advantages
Rapid Prototyping and Customization
One of the primary benefits of sheet metal fabrication is the ability to quickly produce prototype parts with high precision and speed. This allows for immediate adjustments to designs, making the process flexible and cost-effective when creating custom parts. As production volumes increase, the cost per part decreases significantly, leading to substantial savings and consistent results across high-volume outputs.
Enhanced Productivity through Industry 4.0
The integration of Industry 4.0 technologies in sheet metal fabrication can significantly boost productivity and efficiency. Automation of repetitive tasks, alongside smart machines and IoT connectivity, allows for streamlined workflows, reduced downtime, and enhanced output levels without sacrificing quality. This technological advancement translates into improved overall performance in manufacturing processes.
Improved Design Quality
The use of Computer-Aided Design (CAD) tools has revolutionized the design phase in sheet metal fabrication. These tools enable better design quality and accuracy, minimizing material waste and allowing designers to visualize the final product without the need for extensive assembly.
Sustainability Practices
Implementing environmentally friendly practices, such as recycling scrap metal and optimizing material usage, not only reduces waste but also enhances a company’s public image and regulatory compliance. Energy-efficient technologies further contribute to sustainability efforts within the metal fabrication industry.
Disadvantages
Initial Costs and Complexity
While the long-term benefits of investing in advanced technologies and automation systems can outweigh initial costs, the upfront investment remains a notable drawback. Cheaper alternatives may lead to higher costs in the long run due to scaling challenges or customization needs. Additionally, the complexity of operating sophisticated machinery requires substantial training and technical know-how from staff, which can complicate initial implementations.
Limitations of Design and Precision
The design requirements for sheet metal fabrication can pose limitations, particularly for intricate geometries. While simple designs may require fewer processes, complex shapes necessitate more elaborate manufacturing techniques, increasing production time and costs. Tolerance levels must also be carefully managed, as higher precision typically demands more resources and can introduce inconsistencies if not handled correctly.
Automation Challenges
Automation in sheet metal fabrication, while beneficial, presents challenges, especially when managing low-volume, high-variety production. The initial setup costs and programming requirements for automated systems can be significant, and without the appropriate product mix, the advantages of automation may not be fully realized.
Industry
Overview of the Sheet Metal Fabrication Industry
The sheet metal fabrication industry plays a crucial role in various sectors, including automotive, aerospace and defense, and semiconductor manufacturing. These key industries heavily rely on advanced metal fabrication equipment to ensure efficient material handling, reduce operating costs, and shorten cycle times. As a result, the demand for high-quality fabrication techniques continues to grow, driven by the industry’s dependence on technological advancements and the need for customization.
Impact of Industry 4.0
The advent of Industry 4.0 has marked a transformative shift within the manufacturing landscape, including sheet metal fabrication. This fourth industrial revolution encompasses the integration of automation, data exchange, and digital technologies, creating a more interconnected and intelligent manufacturing environment. The benefits of adopting Industry 4.0 solutions in sheet metal fabrication include enhanced productivity, the ability to customize products, and the development of new business models, all of which contribute to improved profitability.
Technological Advancements
The growth of the Metal Fabrication Equipment Market is significantly influenced by advancements in automation and precision metal machining, which are essential for mass manufacturing. The rise in digital technologies and industrial computerization has enabled manufacturers to optimize production processes, thus reducing scrap and enhancing overall efficiency.
Customization and Efficiency
The industry is also experiencing a shift towards customization, allowing manufacturers to cater to individual customer needs while maintaining streamlined production processes. Techniques such as just-in-time manufacturing are employed to reduce lead times and optimize inventory management, thereby achieving a balance between mass production efficiency and personalized offerings.
Future Outlook
Looking ahead to 2024 and beyond, the sheet metal fabrication industry is poised for a paradigm shift characterized by the adoption of digital technologies and a heightened focus on sustainability. Industry players must stay informed and agile in response to emerging trends, as these will be crucial for thriving in an increasingly competitive and complex landscape. As the integration of Industry 4.0 innovations continues, the future of sheet metal fabrication is expected to be defined by innovation, efficiency, and environmental responsibility.