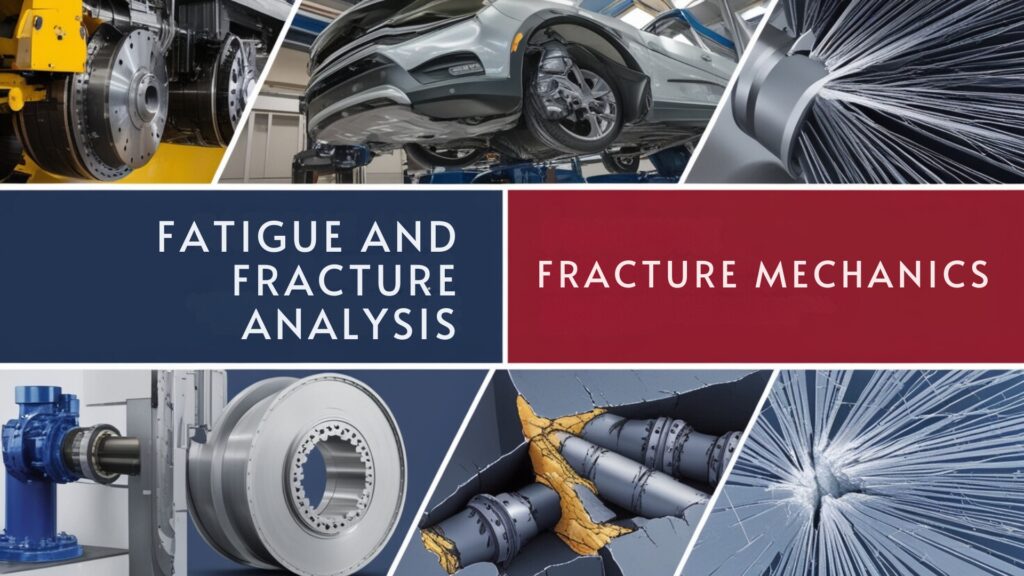
Introduction
Fatigue and Fracture Analysis is a critical field of engineering that examines the mechanisms and implications of material fatigue and fracture under cyclic loading conditions. It encompasses the study of how materials fail when subjected to repetitive stress, leading to structural integrity concerns in various industries, including automotive, aerospace, and civil engineering. The historical significance of this field is underscored by notable failures, such as the 1842 Versailles train crash, which highlighted the need for understanding material behavior and initiated advancements in design and testing protocols.
The study is primarily divided into two key areas: fatigue analysis and fracture mechanics. Fatigue refers to the progressive weakening of materials due to repeated loading cycles, typically categorized into high-cycle fatigue (HCF) and low-cycle fatigue (LCF). Each type exhibits unique failure characteristics influenced by factors such as stress levels, material properties, and environmental conditions. In contrast, fracture mechanics focuses on the analysis of crack initiation and propagation, assessing how flaws in materials can lead to catastrophic failures. Notable controversies within the field include ongoing debates regarding the adequacy of current design codes and standards to adequately address the complexities of fatigue failure, particularly in the context of seismic vulnerabilities in structures.
Historical events, such as the Northridge earthquake in 1994, have prompted significant revisions to engineering practices to enhance the safety and performance of structures under extreme conditions. As material science evolves, particularly with the rise of advanced manufacturing techniques like 3D printing, continuous research is essential to adapt fatigue and fracture analysis methodologies to ensure the reliability and durability of modern engineering applications.
Historical Background
The study of fatigue and fracture mechanics has evolved significantly over the years, influenced by various incidents and advancements in material science. One pivotal event was the Versailles train crash in 1842, which marked a turning point in the understanding of material fatigue. Occurring at a time when metal fatigue was not well understood, the accident led to public fear and confusion regarding the safety of the emerging railroad system. In the wake of this disaster, researchers like William Rankine and August Wöhler dedicated themselves to advancing the design and testing of train axles, highlighting the importance of understanding fatigue and fracture mechanics in engineering.
Significant developments in fatigue analysis began in the early 20th century. O. H. Basquin introduced a log-log relationship for S-N curves in 1910, which became foundational for understanding material endurance under cyclic loading. This was followed by the popularization of the linear damage hypothesis by A. M. Miner in 1945, which provided a practical framework for assessing cumulative damage in materials. As research progressed, the methodologies employed in the field diversified. While analytical and numerical approaches dominated the study of structural fragility, experimental, statistical, and empirical methods were employed less frequently. The period between 2017 and 2019 saw a peak in research on fragility analysis, suggesting a growing interest in this area within the engineering community.
Types of Fatigue
Fatigue manifests in various forms depending on the nature of the stress cycles and the material’s response. Understanding these types is essential for engineers in designing structures and components that can withstand repetitive loading.
Mechanisms of Fatigue
Fatigue in materials is a critical phenomenon characterized by the initiation and propagation of cracks due to cyclic loading. The fatigue process is typically divided into three distinct stages: crack initiation, crack propagation, and ultimate failure. Initially, small cracks form at points of high-stress concentration, often influenced by microscopic defects within the material. As stress cycles continue, these cracks grow incrementally, eventually leading to rapid failure once a critical size is reached.
Stages of Fatigue
The fatigue process comprises three main stages:
- Crack Initiation: This stage involves the formation of tiny cracks, often initiated at defects or stress concentration points. Factors such as the material’s properties, environmental conditions, and the magnitude and frequency of applied stresses can significantly influence this stage.
- Crack Propagation: Once initiated, cracks grow with each loading cycle. This phase consumes most of the material’s fatigue life, with the crack’s propagation rate being influenced by stress levels, mean stress, and environmental factors. The crack will continue to grow until it reaches a critical size, at which point rapid failure can occur without warning.
- Ultimate Failure: This final stage occurs very quickly once the crack has reached a critical size, leading to complete fracture of the material.
Types of Fatigue
Fatigue manifests in various forms depending on the nature of the loading and material response.
- High-Cycle Fatigue (HCF): Involves low-stress levels with a high number of cycles, typically exceeding 10,000 cycles to failure. It often occurs in components subjected to repeated loads, such as bridges experiencing cyclical loading from passing vehicles.
- Low-Cycle Fatigue (LCF): Characterized by high stress and a limited number of cycles, where significant plastic deformation occurs during loading. This type is particularly relevant in applications where components are subjected to large, repeated loads.
- Thermal Fatigue: Induced by thermal cycling, this type of fatigue results from repetitive heating and cooling of materials, which can lead to crack initiation and growth due to thermal stresses.
Factors Affecting Fatigue Behavior
Several factors influence the fatigue behavior of materials, including:
- Type and Nature of Loading: The manner in which loads are applied—whether static, dynamic, or cyclic—affects fatigue life.
- Material Properties: The inherent characteristics of materials, such as grain structure and defect distribution, play a critical role in fatigue resistance.
- Environmental Effects: Conditions such as temperature, humidity, and corrosive environments can significantly impact fatigue performance.
- Stress Concentrations: Geometrical features and imperfections that lead to localized increases in stress can initiate cracks more readily. Understanding these mechanisms and factors is vital for engineers as they design structures and components that can withstand the repeated loading conditions they will face throughout their service life.
Fracture Mechanics
Fracture mechanics is a specialized field of mechanics focused on the study of crack propagation in materials. It utilizes methods from analytical and experimental solid mechanics to assess the driving forces on cracks and the materials’ resistance to fracture. This discipline is crucial for understanding material failure, particularly in engineering applications where flaws are introduced during manufacturing, processing, or machining.
Key Concepts in Fracture Mechanics
Fracture mechanics addresses the nature and stability of flaws found in mechanical components, differentiating between stable and unstable defects under service conditions. The ultimate goal is to ascertain the strength of a component in relation to crack size, as well as to identify mechanisms that prevent spontaneous crack propagation, such as plastic deformation at the crack tip. This deformation is primarily influenced by the applied stress, crack length, and specimen geometry. Irwin’s models provide insights into the plastic deformation zones and their relationships to the stress intensity factors necessary for crack growth.
Types of Fracture Mechanics
Fracture mechanics can be classified into two main categories: linear elastic fracture mechanics (LEFM) and elasto-plastic fracture mechanics (EPFM). LEFM is effective for brittle materials like glass and high-strength steel, while EPFM is applied to ductile materials, where plasticity often precedes fracture. The approach employed is determined by the material properties and loading conditions.
Microscopic and Macroscopic Perspectives
Fracture mechanics also encompasses microscopic fracture mechanics, which investigates fracture at the microstructural level, considering grain boundaries and dislocations. This analysis is vital for comprehending crack initiation and propagation mechanisms through advanced techniques like molecular dynamics simulations. Conversely, macroscopic approaches analyze the overall behavior of structures with geometrical discontinuities, which have become foundational to modern design philosophies, such as damage tolerance in aircraft engineering.
Crack Propagation Stages
The process of crack propagation can be divided into distinct stages. Initially, as a crack grows, it approaches a critical length where the stress intensity at the crack tip reaches a critical value known as fracture toughness. Beyond this point, unstable crack growth occurs, characterized by rapid propagation at high velocities and significant energy release. This can result in either complete fracture, leading to catastrophic failure, or crack arrest under specific conditions.
Experimental Methods
Experimental methods in fatigue analysis involve physically testing materials and structures to observe their fatigue behavior under controlled conditions, providing essential data to validate analytical models and ensure the reliability of fatigue predictions.
Key Testing Methods
Rotating Bending Test
This test subjects a cylindrical specimen to a rotating bending load, generating a cyclic stress distribution. It is primarily used to determine the material’s fatigue limit and the number of cycles to failure under bending conditions.
Axial Fatigue Test
In this test, a specimen is subjected to repeated axial loads (tension-compression) to simulate real-world conditions where components experience direct pull and push forces. The axial fatigue test measures the material’s response to fluctuating axial stresses, providing insights into its durability under repeated loading.
Crack Growth Testing
Crack growth testing involves monitoring the growth of a preexisting crack in a material under cyclic loading. This method helps understand the rate of crack propagation and the factors influencing it, such as stress intensity and environmental conditions.
High-Frequency Resonance Testing
This technique applies cyclic loads at high frequencies to accelerate the fatigue testing process. It is particularly beneficial for materials that require millions of cycles to reach fatigue failure, enabling a quicker assessment of fatigue life.
Thermal Fatigue Testing
Thermal fatigue testing subjects specimens to cyclic thermal loads to replicate conditions where materials experience repeated heating and cooling. This test is critical for evaluating materials used in high-temperature applications, such as turbine blades and exhaust systems. These experimental methods play a crucial role in enhancing the accuracy and efficiency of fatigue assessments, thereby ensuring that materials and structures meet safety and performance standards in real-world applications.
Applications
Automotive Industry
Within the automotive sector, fatigue testing is essential for evaluating materials like polymer matrix composites (PMC) and carbon fiber reinforced polymers (CFRP). These materials, commonly used in vehicle manufacturing, pose unique challenges due to their anisotropic properties, which affect their fatigue performance based on the direction of applied loads. Consequently, advanced testing techniques are required to ensure their reliability under various conditions. Manufacturers are increasingly exploring life prediction methodologies to enhance material properties and overall vehicle performance, indicating a shift towards more innovative engineering practices.
Structural Engineering
Fatigue and fracture analysis play a critical role in structural engineering, particularly in the design and assessment of bridges. Following significant earthquakes, research has focused on improving the seismic resistance of highway bridges by updating design guidelines and retrofitting existing structures. This involves assimilating data from past seismic events, such as the Northridge and Loma Prieta earthquakes, and employing analytical techniques to enhance bridge safety standards. For instance, the incorporation of seismic isolation technologies can mitigate damage to bridges with short, stiff columns, thus improving their performance during seismic activities.
Research and Development
Research initiatives often focus on the applicability of various fatigue analysis methods, including stress-life (SN) and strain-life (EN) approaches, to solve real-world engineering problems. Training programs have been developed for engineers to gain hands-on experience with these methods, thereby reinforcing their practical application in design and analysis roles. The ongoing evolution of materials, such as the rise of 3D printing technologies, further underscores the need for continuous research in fatigue and fracture analysis to adapt to new manufacturing techniques and their implications for product durability.
Seismic Vulnerability Assessment
Assessing the seismic vulnerability of structures, particularly cable-stayed bridges, is crucial due to their flexibility and susceptibility to earthquake-induced forces. Studies have shown that the performance of these bridges can be significantly affected by design factors such as pier height and cross-section, highlighting the need for targeted evaluations and retrofitting strategies to enhance their resilience. Comprehensive methodologies for assessing earthquake resistance and addressing the degradation caused by factors like reinforcing steel corrosion are critical in ensuring long-term safety and functionality of bridge infrastructures.
Failure Analysis
Overview of Fatigue Failure
Fatigue failure is a critical concern in engineering design, characterized by the progressive initiation and growth of cracks under repeated cyclic stress loading. This phenomenon often leads to structural failure at stress levels significantly below the material’s yield or ultimate strengths. It is estimated that the annual economic cost associated with fatigue failure in the U.S. alone was around $100 billion in 1982 dollars, reflecting its impact across various sectors including ground and rail vehicles, aircraft, and infrastructure.
Mechanisms of Fatigue Failure
Fatigue failures can occur due to several factors, including design inadequacies, material defects, and environmental uncertainties. The mechanisms involve the formation and propagation of cracks until they reach a critical size, resulting in fracture. Fracture mechanics plays a vital role in understanding these processes, as it analyzes flaws in materials to determine which are safe and which may lead to catastrophic failure. The study of these mechanisms has gained prominence over the past century, allowing engineers to develop methodologies aimed at predicting and mitigating the risk of fatigue failure.
Importance of Design Considerations
Effective design strategies must consider a range of factors that could contribute to fatigue failure, particularly in safety-critical applications. This includes accounting for potential flaws introduced during manufacturing, such as interior and surface defects, and ensuring that structures can tolerate expected loading conditions. Techniques like damage tolerance analysis and fracture toughness testing have been developed to enhance the safety and longevity of engineering designs.
Case Studies and Practical Applications
Historical events, such as the 1994 Northridge earthquake, have highlighted the necessity of understanding fatigue and fracture mechanics. The earthquake revealed numerous fractured connections in steel structures, prompting revisions in building codes and increased focus on damage tolerance principles. This illustrates the practical implications of fatigue analysis in civil engineering, where applying theoretical principles can enhance safety and performance in real-world scenarios.
Limitations and Future Directions
Despite advancements in design codes, several limitations persist, particularly regarding the assessment of structural responses under seismic loading. Current codes often lack provisions for maximum allowable displacements in critical components, which can lead to increased risks during seismic events. Research continues to address these gaps by exploring innovative design methodologies and materials that can withstand cyclical stresses more effectively. The ongoing evolution of analytical techniques, including inelastic, nonlinear analyses, is essential for improving performance-based design methodologies in the future.
Standards and Guidelines
Seismic Design Guidelines
The development of national bridge seismic design guidelines began in 1971 under the Federal Highway Administration (FHWA), with an initial budget of $3 million dedicated to basic research. The program aimed to evaluate existing seismic design criteria, incorporate recent seismic research findings, and create new design guidelines. These guidelines were finalized in 1979 and adopted by the American Association of State Highway and Transportation Officials (AASHTO) as the Guide Specification for Seismic Design of Highway Bridges in 1983. This specification became the national standard in 1992, notably influenced by the Loma Prieta earthquake.
Fragility Analysis Methods
Fragility analysis plays a crucial role in assessing the vulnerability of structures to various hazards.
- ATC-40: Developed by the Applied Technology Council, this method assesses the seismic vulnerability of buildings.
- ASCE 41: This method, created by the American Society of Civil Engineers, evaluates the seismic performance of existing structures.
- FEMA P-58 and FEMA 356: Both methods, developed by the Federal Emergency Management Agency, are utilized to assess the seismic performance of buildings and other structures.
- ASCE 7–16: This standard is used to determine design loads for buildings, including seismic, wind, and snow loads.
Structural Design Standards
Various standards guide the design of structural materials:
- AISC 360: This standard pertains to the design of steel structures and includes provisions for stability, strength, and ductility.
- ACI 318: This guideline is focused on the design of concrete structures, emphasizing stability, strength, and durability.
- Eurocode 8: This set of European standards provides comprehensive guidelines for the seismic design of structures, ensuring a uniform approach across member states.[11]
Emerging Technologies in Design
Additive Manufacturing (AM) has significantly influenced modern design methodologies, particularly in aerospace engineering, where it allows for the creation of lightweight and high-performance structures. The technology provides unprecedented design freedom, enabling engineers to create previously unfeasible lattice structures. Understanding fatigue strength and predicting fatigue life in both low cycle fatigue (LCF) and high cycle fatigue (HCF) scenarios has become essential for ensuring safety and reliability in aerospace systems.
Future
Advancements in Material Design
The future of fatigue and fracture analysis is heavily tied to innovative approaches in material design. Research is focusing on developing predictive models that estimate the life expectancy of materials, which is crucial for enhancing safety and efficiency in various applications, particularly in aerospace engineering. These predictive models aim to minimize discrepancies between predicted and actual lifespan, thereby improving the reliability of material performance.
Integration of New Technologies
The emergence of new manufacturing techniques, such as 3D printing, poses both challenges and opportunities in the realm of fatigue and fracture analysis. While these methods can enhance material properties and performance, they also complicate the ability to predict fatigue resistance accurately. As research progresses and more data becomes available, the adoption of these advanced materials is expected to increase, allowing manufacturers to refine their processes and enhance product quality.
Seismic Design Considerations
Future research will also likely emphasize the importance of seismic design and retrofitting in civil engineering. Balancing these design approaches is essential for fortifying infrastructure against seismic events. This involves upgrading critical structures while also adhering to updated seismic design standards for new constructions. By implementing such measures, the risk of structural damage can be significantly reduced, contributing to safer highways and bridges.