An Introduction to the Valve Timing Diagram
The valve timing diagram of 4 stroke engine is a 360-degree diagram that depicts the piston’s movement from TDC to BDC in all strokes of the engine cycle, which is measured in degrees, and the valves are opened and closed following these degrees. We often say things like “The air-fuel mixture combusts to create piston movement, which causes crankshaft rotation,” and “The fraction of the combustion escapes through the exhaust,” but have you ever wondered how these intake and exhaust mechanisms work? How are the intake and exhaust timing controlled? But how are these intake and exhaust valves managed, one would wonder? Let’s have a look at it and see what we can find.
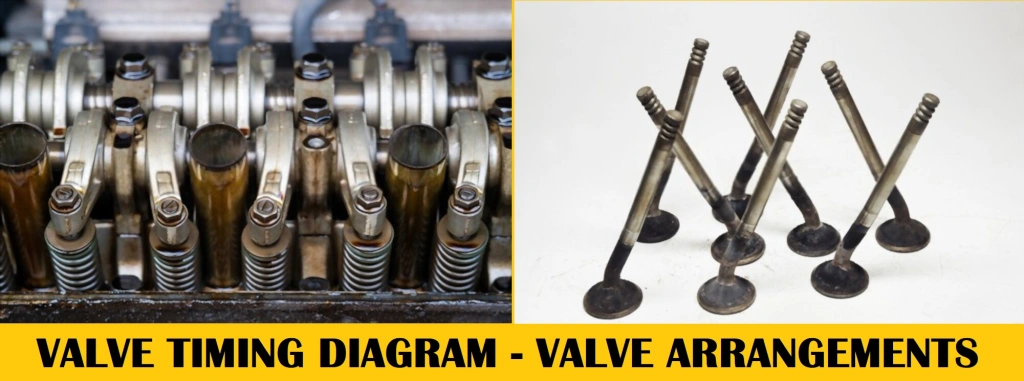
What is the valve timing diagram?
We consider that for the valve timing diagram, the valves open and close at the dead center positions of the piston. But, in actual practice, they do not open and close instantaneously at dead centers. The valves operate to some degree before or after the dead centers. The ignition timing is also timed to occur a little before the top dead center. The timing of these sequences of events can be shown graphically in terms of crank angles from the dead center position. This diagram is known as the valve timing diagram.
Why do We Need a Valve Timing diagram?
Because a single cycle (from the intake of the air-fuel mixture to the exhaust of the combustion residue) of an internal combustion engine completes roughly 100000 cycles per minute, it is important to be provided with an effective system that can operate.
- Synchronization between the phases of an engine cycle, from the air-fuel ratio intake through the residual combustion exhaust.
- Complete seizure of the combustion chamber at the point when the air-fuel combination is ignited, as leaking can harm the engine and be dangerous.
- When the engine requires it (at the moment of suction), provide it with a mixture of air and fuel or air in the case of a diesel engine.
- Allow the combustion residue to leave so that the engine can complete its next cycle.
- The timing of the opening and closing of the intake and outlet valves is perfect, which protects the engine against knocking and explosion.
- To burn the fuel, a high compression ratio is necessary, especially in the case of a diesel engine, which is accomplished by overlapping the valve closings.
- The cleaning of the engine cylinder improves combustion quality and reduces wear and tear inside the cylinder.
- The investigation of the specifics of combustion is essential for modifying the engine’s power.
As a result of these factors, the engine, whether 2-stroke or 4-stroke, is constructed according to the valve timing diagram, so that the piston moves from TDC to BDC is accompanied by the optimal timing of the intake and exhaust valves opening and closing.
Nomenclature in the valve timing diagram of Four-stroke Engines
Top Dead Center (TDC):
Set the piston where it comes to a complete halt away from the crankshaft. This position is called top because it is towards the top of the engines (but not usually), and dead because the piston comes to a halt here. TDC is not always at the top of the engine’s priority list (e.g: horizontally opposed engines, radial engines, etc,.) The clearance volume is the smallest volume in the cylinder when the piston is at TDC.
Bottom Dead Center (BDC):
The piston’s position when it comes to a halt closest to the crankshaft. Because it is not always at the bottom of the engine, some publications refer to it as Crank End Dead Center (CEDC).
Stroke (L) :
TDC to BDC or BDC to TDC is the distance traversed by the piston from one extreme position to the other.
Compression ratio (r) :
The compression ratio of an engine is the ratio of overall volume to cylinder clearance volume. SI engines have compression ratios ranging from 8 to 12, whereas CI engines have compression ratios ranging from 12 to 24.
Configuration of petrol and diesel engines
- Vertical Engines
- Horizontal Engines
- Inline Engines: A single row of cylinders is placed in a line.
- V Engines: Two rows of cylinders are positioned at an angle to one another.
- Opposed Cylinder Engines: On opposing sides of the engine, two rows of cylinders are placed.
- Radial Engines: Around the common crankshaft, the cylinders are positioned radially and evenly spaced.
The valve timing diagram for 4 stroke petrol engine:
The diagram shows the valve timing diagram for a four-stroke cycle petrol engine. The inlet poppet valve opens 10–30° before the top dead center position. The air fuel mixture is sucked into the engine cylinder till the inlet valve closes. The inlet valve closes 30–40°, or even 60° after the bottom dead center position. The airfuel mixture is compressed till the spark occurs.
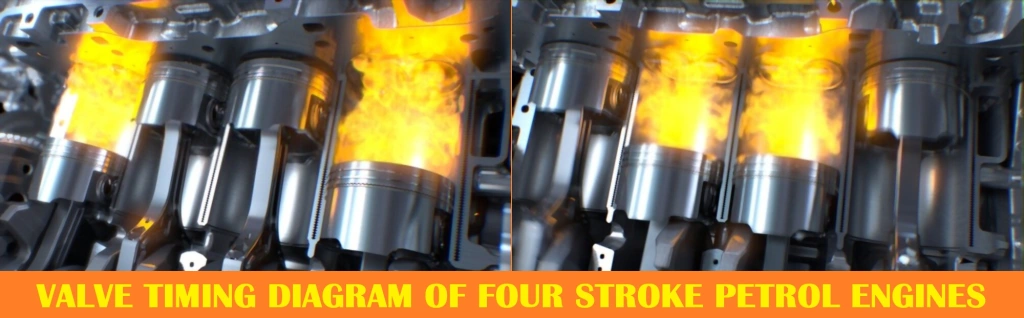
The theoretical valve timing diagram for 4 stroke engines
A valve timing diagram for a 4 stroke cycle petrol engine is shown in the diagram. The input valve opens 10–30 degrees before the top dead center. Until the intake valve shuts, the air-fuel mixture is sucked into the 4 stroke cycle engine cylinder. After reaching the bottom dead center position, the input valve shuts 30–40 degrees or even 60 degrees. Until the spark happens, the air-fuel mixture is compressed.
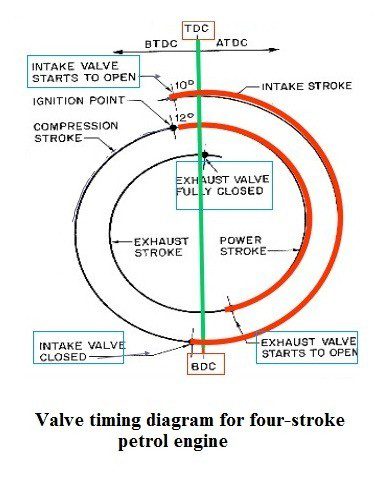
The spark is produced at 20–40° before the t.d.c. position. This gives sufficient time for the fuel to burn. The pressure and temperature increase. The burning gases expand and force the piston to do useful work. The burning gases expand till the exhaust valve opens. The exhaust valve opens 30–60° before the b.d.c. position. The exhaust gases are forced out of the cylinder till the exhaust valve closes. The exhaust valve closes 8–20° after the t.d.c. position. Before it closes, the inlet valve opens 10–30° before the t.d.c. position.
The period between the inlet valve opening and exhaust valve closing is known as the valve overlap period. The crank angle between the inlet valve opening and exhaust valve closing is known as the angle of valve overlap.
Suction Stroke-
The engine cycle begins with this stroke, when the inlet valve opens as the piston advances from TDC to BDC, allowing air-fuel mixture in petrol engines and fresh air in diesel engines to enter the cylinder until the piston reaches BDC.
Compression Stroke-
Following the suction stroke, the piston moves from BDC to TDC to compress the air-fuel mixture (petrol engine) and fresh air (diesel engine), raising the pressure inside the cylinder, which is necessary for the fuel to burn.
- During this action, the inlet engine valve closes to seal the chamber and allow the fuel to be compressed.
Expansion Stroke-
After the fuel is compressed, it is burned, which causes the piston to move from TDC to BDC in order to relieve the pressure created by the combustion, and output is achieved.
Note – The spark created by the spark plug causes combustion in a petrol engine.
- The air and fuel charge enters the cylinder during the suction stroke of a petrol engine.
- Combustion happens in a diesel engine owing to the strong compression supplied by the compression stroke, which is responsible for raising the temperature within the cylinder to the diesel and air charge’s auto-ignition temperature.
- During the suction stroke of a diesel engine, new air enters the cylinder, and the fuel is sprayed over the air by the fuel injectors.
Exhaust Stroke-
Following the expansion stroke, the piston at BDC begins to move towards TDC, which is followed by the opening of the exhaust valve to remove the combustion residue.
- When the piston approaches TDC, the exhaust valve closes.
Actual Process of a valve timing diagram for 4-Stroke engines
- The inlet valve opens 10-20 degrees ahead of TDC in the suction stroke of a 4-stroke engine for proper intake of air-fuel (petrol) or air (diesel), as well as cleansing of leftover combustion residues in the combustion chamber.
- The compression stroke begins when the piston hits BDC, and the piston begins to move back towards TDC. During the compression stroke, the inlet valve closes 25-30 degrees past the BDC, completely sealing the combustion chamber for air-fuel (petrol engine) and air compression (diesel engine).
- The burning of gasoline occurs 20-35 degrees before TDC during the compression stroke as the piston travels towards TDC, ensuring adequate fuel combustion and flame propagation.
- The expansion strokes begin with the burning of fuel, which releases pressure inside the combustion chamber and allows the crankshaft to rotate. During the expansion stroke, which is continuous 30-50 degrees before BDC, the piston advances from TDC to BDC.
- The exhaust valve opens 30-50 degrees before BDC, which starts the exhaust stroke, and the combustion residue is expelled as the piston moves from BDC to TDC, which continues for another 10-20 degrees after the piston valve reaches TDC.
As can be seen throughout the cycle, the SI engine valves overlap twice, with both valves shutting during the compression stroke and both piston valves opening during the exhaust stroke.
Reasons for Actual valve timing diagram
Mechanical and dynamic factors are the two components that control valve timing.
- Mechanical Factor: – Because valves are controlled by cams, they cannot be opened and closed abruptly. As a result, the valve must be opened ahead of schedule. The valve opening and closing times are stretched over a large number of crankshaft degrees of rotation to reduce noise, wear, and impact hitting the valve on the valve seat. As a result, the valve opening must begin ahead of schedule.
- Dynamic Factor: The actual valve timing is determined by taking into account the dynamic impacts of exhaust gas flow in addition to the mechanical engineering aspect of opening and closing valves
The valve timing diagram for a four-stroke diesel engine:
The actual valve timing diagram for a four-stroke diesel engine is shown in the figure. The inlet valve opens 10-25° before the top dead center position. Fresh air is sucked into the engine cylinder till the inlet valve closes. The inlet valve closes 25–50° after the bottom dead center position. The air is compressed till the fuel is injected. The fuel injection starts 5–10° before the t.d.c. position in the compression stroke. The air-fuel mixture burns. The temperature and pressure increase.
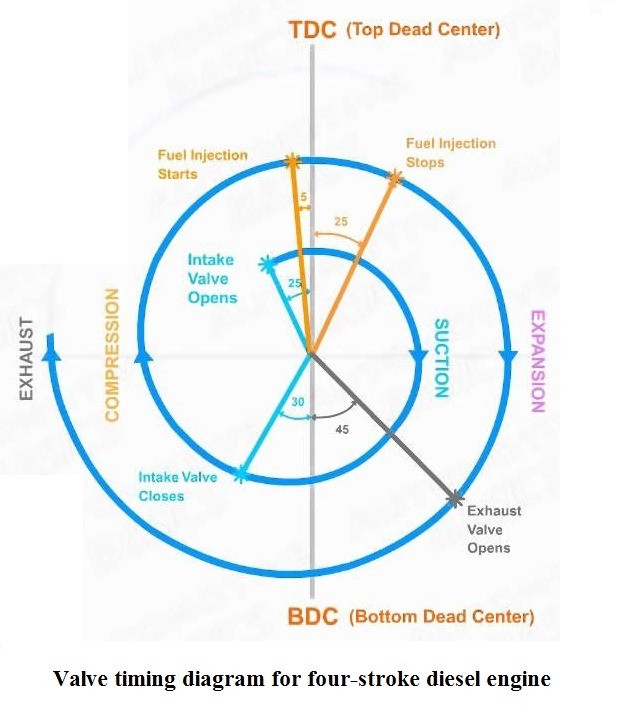
The burnt gas expands till the exhaust valve opens. The exhaust valve opens 30–50° before the b.d.c. position. The exhaust gases are forced out of the engine cylinder till the exhaust valve closes. The exhaust valve closes 10-15° after the t.d.c. position. Before the exhaust valve closes, the inlet valve opens 10–25° before the t.d.c. position. The period between the inlet valve opening and the exhaust valve closing is known as the “valve overlap period.” The angle between these two events is known as the angle of valve overlap.
Port Timing Diagram for 2-Stroke Engine
In a 2-stroke petrol engine, the engine cycle is completed in two strokes, namely the expansion and compression strokes. The fuel input and combustion residual exhaust occur during these two strokes, respectively.
Theoretical port timing
Expansion stroke-
The piston, which is at TDC at the start of the expansion stroke, begins to move towards BDC owing to the combustion of compressed air-fuel (petrol engine) and (diesel sprayed charge in a diesel engine) during the compression stroke, resulting in the power output.
- During the expansion strokes, the air-fuel (petrol engine) and air (diesel engine) enter through the inlet port as the piston advances from TDC to BDC.
- Until the piston hits BDC, the expansion stroke continues indefinitely.
Compression Stroke-
Due to the movement of the piston from BDC to TDC at the completion of the expansion stroke, compression of air-fuel (petrol engine) and diesel sprayed charge (diesel engine) begins, along with the emission of combustion residue via the exhaust port.
- As the piston moves from BDC to TDC, it closes both the intake and exhaust ports, increasing the pressure inside the combustion chamber.
- When the piston reaches TDC at the end of the compression stroke, combustion of the air-fuel (petrol engine) and diesel sprayed charge (diesel engine) occurs owing to high pressure, and the cycle repeats.
Actual or practical process
- The intake port opens 10-20 degrees before the piston hits TDC, starting the expansion stroke owing to combustion of air-fuel (petrol engine) from the crankcase and air (diesel engine) entered via the inlet port, pushing the piston towards BDC.
- During the 2-stroke engine’s expansion stroke, the intake port closes 15-20 degrees after TDC.
- Because the piston moves from TDC to BDC during the expansion stroke, the exhaust port opens 35-60 degrees before the piston reaches BDC, allowing the combustion residue to be ejected.
- For the scavenging phase, open the transfer port 30-45 degrees before the BDC.
- The scavenging process is stopped when the piston advances from BDC to TDC and the transfer port closes 30-45 degrees after BDC.
- The exhaust valve closes 35-60 degrees after BDC, blocking the combustion chamber, and pressure inside the combustion chamber rises owing to the commencement of the compression stroke as the piston moves from BDC to TDC. The cycle begins once more.
- During the opening of the transfer port, the air-fuel mixture (petrol engine) and air (diesel engine) are both transferred to the cylinder.
Note – The opening and closing of valves a few degrees before TDC and BDC is essential for normal engine functioning because these degree gaps ensure appropriate stroke completion, avoid engine flaws such as knocking, and reduce emissions.
- This valve timing is altered for power modification, which boosts the engine’s power and torque while decreasing its efficiency.
Variable Valve Timing
Variable Valve Timing is the next step in improving engine output, regardless of power or torque, once multi-valve technology became mainstream in engine construction.
Valves are responsible for the engine’s breathing. The shape and phase angle of cams affect the timing of breathing, that is, the timing of air intake and exhaust. The engine requires variable valve timing at various speeds to maximize breathing. As the revolutions rise, the duration of the intake and exhaust strokes shortens, preventing fresh air from entering the combustion chamber and exhaust from leaving the combustion chamber quickly enough. As a result, opening the inlet valves first and closing the exhaust valves subsequently is the optimum choice. In other words, when rpm rise, the overlap between the intake and exhaust periods should increase.
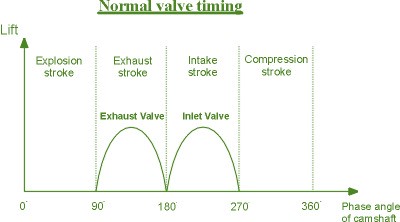
The Function of the VVT System
Because the speed of automobile engines varies, the timing diagram should ideally fluctuate as well. In other words, depending on the engine speed, the valve closing and opening angles should be adjusted to maximize the cylinder emptying and filling operations.
A phase shifter situated at the head of the camshaft is used by the VVT system to modify valve timing. The engine control unit activates this component by controlling oil flow through a solenoid valve.
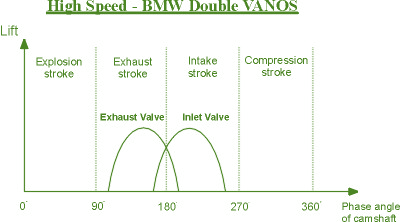
The following are the key benefits of a Variable valve timing system:
- fuel usage is lower
- torque and power increase
- emission reductions
Latest advancements in VVT system mainly in Petrol Engines
In the late 1980s and early 1990s, the VVT technology was adopted in Asian and European automobiles. This system grew in popularity in the mid-2000s, and all of the major automakers began to utilize it. This system is now often present in petrol engines, and it is also found in certain diesel engines. While the name given to the system varies from one manufacturer to the next, and there may be minor modifications, the basic principle of functioning remains the same:
- Honda: VTEC
- Toyota: VVT-i
- BMW: VANOS
- Ford: Ti-VCT
- Kia-Hyundai: CVVT
- Porsche: VARIO CAM
- VAG: TGV
Engineers used to determine the optimal compromise time without Variable Valve Timing technology. For example, a van’s low-speed output may necessitate less overlapping. For high-speed power, a racing engine may use a lot of overlapping. Valve timing optimized for mid-rev may be used in a regular car to ensure that low-speed drivability and high-speed output are not compromised too much. Regardless of whether the method is used, the end output is always optimized for a specific pace.
Power and torque may be adjusted throughout a wide rpm range with Variable Valve Timing. The following are the most notable outcomes:
- The engine’s top speed may be increased, resulting in more peak power. Nissan’s 2-litre Neo VVL engine, for example, produces 25% greater peak power than its non-VVT counterpart.
- As low-speed torque increases, drivability improves. The 1.8 VVT engine in the Fiat Barchetta, for example, produces 90 percent peak torque between 2,000 and 6,000 rpm.
FAQs on Valve Timing Diagram
Valve overlap is the number of degrees of crankshaft rotation during which
- Both intake and exhaust valves are closed
- Both intake and exhaust valves are open
- The valves are moving from fully closed to the timing point
- The valves float
Answer: both intake and exhaust valves are open
Explanation:
- Both the intake and exhaust valves are open during a section of a reciprocating engine’s working cycle when the piston reaches TDC on the exhaust stroke.
- The amount of degrees of crankshaft rotation during which both the intake and exhaust valves are open is known as valve overlap.
- The low pressure created by exhaust gases (leaving the cylinder) helps the new fresh charge of the fuel-air combination to start flowing into the engine, which boosts the engine’s efficiency.
- Valve timing refers to how the valves open and closes in an IC engine in relation to the piston and flywheel movement.
- A diagram on the face of the flywheel depicts the valve timing in degrees of crankshaft rotation.
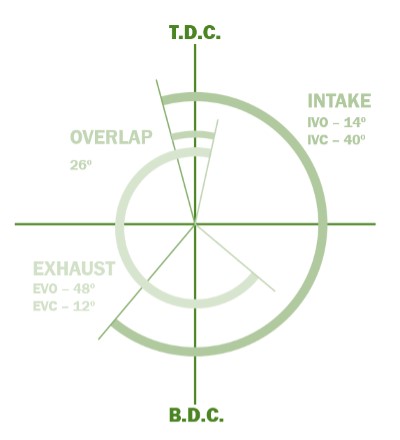
Valve timing diagram:
- 9 degrees before TDC, the inlet valve opens.
- After BDC, the inlet valve closes 50 degrees.
- Before BDC, the exhaust valve opens 47 degrees.
- After TDC, the exhaust valves close 12 degrees.
- Period of overlap: 21 degrees
What are the two most important elements that influence valve timing?
It can be changed by changing the camshaft or by changing the valve timing while the engine is running. It is also influenced by the valve mechanism’s adjustment, notably the tappet clearance.
What happens if the timing chain of the valves isn’t proper?
Not only can the engine fail to start if the valve timing is improper, but the piston may also crash into the valves, inflicting catastrophic damage. Slide valve bends and piston damage are common outcomes.
When it comes to engine performance, how does valve timing play a role?
High-RPM engines require a faster opening of the exhaust valve to allow the pressure to escape the cylinder. At lower RPMs, though, opening the exhaust valve too quickly means you’re not getting the most out of the power stroke.
What is the procedure for adjusting valve timings?
Loosen the locknut using a ring spanner and move the screw clockwise to narrow the gap and counterclockwise to widen it. When the clearance is tight, tighten the locknut while holding the screw with a screwdriver, then re-check the clearance. There may be no locknut on a self-locking adjustment screw.
What happens if the clearance between the valves is too large?
Because the engine can’t “breathe” properly and function at full efficiency, too much or too little valve clearance might produce poor performance or a harsh idle. Too much space causes the valves to clatter, which can harm the valves, camshaft lobes, and rocker arms in the long run.
What is the significance of valve timing in all engines?
Valve timing is an important aspect of the internal combustion process because it controls the flow of fuel and air into and out of the combustion chamber, which is where the pistons compress the fuel and air for burning.
When your valves are too tight, what happens?
The valve lead will never fully close as they should if the valve clearance is too tiny. As a result, a portion of the valve surface will be burned away, resulting in a misfiring engine. However, if the valves are excessively tight, the engine operation may run rough, whether cold, hot, or all of the time.
How can I tell whether my bike’s valves need to be adjusted?
The valves won’t shut correctly if the valve train is too tight, and the engine won’t be able to perform at its best. If your bike has adjustable valve clearances, there will be a service interval indicated for them in one of the manuals, generally every 10,000 kilometers.
Do you adjust the valve setting in hot or cold conditions?
To minimize improper adjustments on lifters that have been “pumped up,” most camshaft manufacturers suggest setting valves cold. Before you start setting valves on a new engine that hasn’t been running, make sure everything is fully oiled.
Conclusion
Did you learn about the valve timing diagram of two-stroke and four-stroke petrol and diesel engines in this post? If you find this material useful, please share it on social media.